Growing Together Summer 2024
The Role of ResponsibleAg in the Grow West Safety Culture
Everyone who sets foot on a Grow West location goes home at the end of the day in as good or better shape as when they arrived. That’s the goal of and inherent drive behind the Grow West safety culture. Regulatory compliance is important, but the inspiration and necessity behind it — the safety of Grow West employees and customers alike — is why the company participates in and leads the work of ResponsibleAg, including audits that ensure facilities are staying on top of all potential safety issues.
The Owensboro, Kentucky-based organization was born when the Agricultural Retailers Association and The Fertilizer Institute came together to strengthen ag retail facility safety nationwide after a Texas fertilizer plant exploded in 2013. Organizers — including Grow West Vice Chairman Johnny Council and Vice President for Regulatory Affairs David Ito — saw the need for a new initiative that could help develop new nationwide standards to contribute to both safe operations and strong regulatory compliance.
Those standards and the audits that ensure they’re being followed weren’t intended to penalize ag retailers for safety oversights. Instead, they are meant to alert location managers like Grow West’s Tim Johnson of areas where the Talmage and Lakeport locations he manages can make changes to improve safety even further. For Johnson, it was an educational process that helped him make his facilities safer through action and overall safety awareness and vigilance.
“I was relatively new to Grow West when our audit took place, and I learned a lot about our facilities in the whole process. We were able to review processes, equipment and facility designs to ensure maximum safety,” Johnson said. “The ResponsibleAg audits help us stay ahead of potential regulatory issues and, more importantly, enable us to keep our focus where it should be, taking care of our customers and employees.”
Best practices, not penalties
The ResponsibleAg audit process focuses primarily on best management practices. Along with MVP Safety Professionals, an organization co-owned by Grow West that provides safety training and compliance services to Northern California ag producers and affiliated businesses, ResponsibleAg and its audits are part of the Grow West safety culture Ito helps oversee. Requirements for ResponsibleAg audit compliance are based on federal and state regulations, so they enable location managers like Johnson to take corrective action before compliance issues arise. Each Grow West location has a safety committee that regularly monitors safety practices and ensures all regulatory requirements are met. Those committees ladder up to a state-level committee with Western Plant Health, then to the national level with ResponsibleAg. The Ag Retailers Association (ARA) also supports the work of ResponsibleAg.
“When I came into this business 40-plus years ago, we didn’t have regulations like we do today. Now, between our own safety teams and ResponsibleAg audits, we can create a knowledge base for everyone, so they know what needs to happen from a safety standpoint. It’s all about risk mitigation. That’s the goal for everybody,” Ito said. “In a nutshell, we’re really looking out for our customers, employees, the environment and the communities where we work and live.”
What’s covered in a ResponsibleAg audit
Each ResponsibleAg audit is thorough and in-depth, focusing on everything that could potentially lead to personal health and safety risks. For Grow West, that means a close examination of everything from fertilizer and chemical storage and distribution systems to buildings, vehicles and electrical wiring. Each audit covers both facilities and equipment as well as behavioral safety for workers. The audit checklist is broken into 17 sections for inspection and includes a listing of all maintenance records and worksheet in which each facility’s employee training programs are listed. Finally, the document includes a list of best management practices for each category examined during an audit.
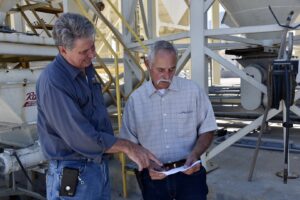
The last portion of the checklist is what elevates the ResponsibleAg audit process compared to similar exercises. Sharing those best management practices when an audit is conducted enables auditors like Grow West Safety Manager Cole Trouberman to facilitate quick corrective action whenever an audit uncovers a potential compliance issue.
“An audit calls out regulatory compliance, but it also addresses things like employee training, then goes into the details on how to best train employees so they operate safely,” Trouberman said, adding audits are typically customized for each facility based on its specific service and product offerings. “The audit process helps paint a clear picture of how regulations and safety are tied together. Because ResponsibleAg is an industry-led initiative, it is practical and based on a lot of collective industry experience.”
How a ResponsibleAg safety audit happens
Trouberman said the ResponsibleAg audit process is about observing and listening. By asking open-ended questions about specific things like how fertilizer is stored, he’s able to not just point out any concerns but provide constructive feedback that leads to improved safety.
“I always start by listening. Sometimes there’s hesitancy to make changes, but we can help prevent safety issues by being proactive rather than reactive,” he said. “I always try to be completely transparent and communicate all of my knowledge of the regulations, but we also work really hard to boil down those regulations so it’s clear and easy to understand why they exist and what they mean to operational safety.”
What’s a ResponsibleAg audit like for an ag retail facility manager? The organization’s not the only auditor for such facilities; Johnson is also audited by the Mendocino County Health Department and Food and Drug Administration (FDA), as well as by some crop protection product manufacturers. So, while he’s no stranger to the process, the relatively new manager quickly saw major differences between those other audits and the one conducted by ResponsibleAg.
“It’s a little scary to have an auditor come. I worry about whether there are things I’m not aware of that we need to be doing. We learn from the process and take the right corrective action,” Johnson said. “The ResponsibleAg audits are rigorous and help educate us on what we can do better. It helps us stay on the straight and narrow.”
The long-term benefits of ResponsibleAg safety audits
The completion of corrective measures to improve facility safety is the benefit to an ag retailer going through the ResponsibleAg audit process. But longer-term benefits further stretch the more immediate objectives. For Johnson and other Grow West location managers like him, the ResponsibleAg process starts building the foundation of safety accountability and self-regulation. That often means subsequent audits uncover fewer compliance issues. That’s a big reason for the strength of the Grow West safety culture; at every level of the company, safety is made an even higher priority than it would have been without the ResponsibleAg audits.
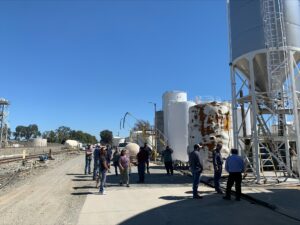
“These audits allow us to proactively self-regulate much better than before. At the end of the day, we are held accountable, and the ResponsibleAg auditor tells me if I’m doing a good job or not. When you know an audit’s coming, you start thinking about whether you’re on the right track,” Johnson said. “Everyone gets it and understands what we need to do to do things as safely as possible. That’s where we start to build that safety culture.”
It’s that culture — one that’s been built over the years at Grow West and continues to advance — that enables Johnson, Trouberman, Ito and everyone else at the company to fulfill the basic safety mission.
“Our biggest priority is making sure our employees go home just the way they came that day because they have people who depend on them not just at work but at home too. That’s so important,” Ito said. “We just want to make sure that they’re going home to their families or loved ones.”
Talk to your local Grow West location manager to find out about the ResponsibleAg audit process.